Managing work at height permits digitally
Create your own Work at Height checklist
Eliminate manual tasks today.
Work at height (WAH) refers to any work activities where there is a risk of falling from one level to another, which could result in personal injury. It includes tasks performed on ladders, scaffolds, platforms, roofs, or any elevated surface such as mobile elevating work platforms (MEWPs), as well as work near openings, holes, or fragile surfaces.
Employers must adhere to specific requirements to ensure the workplace safety and health of those working at height. These requirements may include:
- Conducting a thorough risk assessment before initiating any work at height activities
- Implementing appropriate risk control measures based on the hierarchy of controls (elimination, substitution, engineering controls, administrative controls, and personal protective equipment)
- Developing and implementing a Fall Prevention Plan (FPP) detailing the necessary fall preventive protective control measures and fall hazards
- Ensuring employees receive proper training and are competent to perform work at height tasks
- Providing appropriate personal protective equipment (PPE) and ensure its proper usage
By adhering to relevant WSH regulations and implementing robust permit to work (PTW) systems, employers can create a safer work environment.
Obtaining a Work at Height permit
A Permit to Work (PTW) system is a formal written authorisation process designed to ensure that specific high-risk tasks, such as work at height, are carried out safely and in accordance with established procedures. The PTW system helps identify hazards, evaluate the risk, and implement control measures for safe execution of WAH activities, clearly defining the roles and responsibilities of those involved in the work. A comprehensive PTW system includes the following key elements:
- Identification of tasks requiring a permit
- Assignment of responsible personnel for issuing and receiving permits
- A standardised permit form detailing work scope, hazards, control measures, and responsibilities
- Clear communication of permit requirements and conditions to all relevant parties
- Effective monitoring and control of work activities to ensure compliance with the permit conditions
- Permit close-out and review process to ensure work is completed safely and lessons learned are documented
By implementing a robust PTW system and clearly defining the roles and responsibilities of the issuer and receiver, organisations can effectively manage the risks associated with work at height activities and maintain a safe work environment. To optimise the field processes, many companies today use electronic permits to work.
In addition to the completed permit application form, the documentation required for a work at height permit may include:
- Risk assessment and control measures report
- Fall Prevention Plan (FPP)
- Training and competency records of personnel involved in the work
- Inspection and maintenance records of equipment and PPE
Risk assessment and control measures
Risk assessment involves identifying potential hazards, evaluating the risks, and implementing appropriate control of WAH risk measures to minimise the likelihood and consequences of accidents or injuries.
Employers should conduct a thorough hazard identification process for managing work at height tasks, considering factors such as:
- Working surface conditions (e.g., slippery, uneven, or fragile)
- Weather conditions (e.g., rain, wind, or extreme temperatures)
- Equipment and tools used
- Complexity and duration of the tasks
Once hazards are identified, employers must evaluate the risks by considering the likelihood of an incident occurring and the potential severity of the consequences.
Employers must implement control measures based on the hierarchy of controls, which prioritises the most effective means of risk reduction. The hierarchy, in order of preference, is:
- Elimination: Remove the hazard completely, if possible (e.g., avoid working at height by performing the task at ground level).
- Substitution: Replace the hazard with a less dangerous alternative (e.g., using a safer type of equipment).
- Engineering controls: Implement physical changes to the work environment or equipment (e.g., installing guardrails or platforms).
- Administrative controls: Implement procedural changes, such as work procedures, work at height training, or supervision.
- Personal protective equipment (PPE) for working at height: Provide appropriate PPE, such as harnesses and helmets, as a last line of defence.
By conducting thorough risk assessments and implementing suitable control measures, employers can effectively manage the work at height risks and ensure a safer work environment.
Fall prevention and protection
Fall from height prevention strategies aim to eliminate or minimise and manage the risk of falls during work at height activities. Key strategies include:
- Designing the workplace to minimise the need for work at height
- Implementing appropriate risk control measures (e.g., guardrails, toe boards, or platforms)
- Establishing and enforcing safe work procedures
PPE serves as a last line of defence to protect workers from falls. Common PPE for work at height includes:
- Full-body harnesses
- Lanyards with energy absorbers
- Fall arrest systems, such as retractable lifelines
Employers must provide suitable PPE, ensure its proper usage, and regularly inspect and maintain it.
By implementing effective fall prevention strategies and providing appropriate PPE, employers can reduce the risk of falls and ensure the safety of workers who are required in managing work at height activities.
Training and competency requirements
Proper training is essential to ensure the safety of workers involved in managing work at height activities. Employers must ensure that all relevant personnel receive appropriate training, which may include work at height courses for workers, supervisors and assessors. Here is an example of a short video that can be shared with employees on site during the induction process or toolbox meetings.
Employers must ensure that supervisors, assessors, and trainers involved in work at height activities possess the necessary competencies and qualifications to perform their roles effectively. By providing adequate training, ensuring the successful completion of the courses, and ensuring the competency of all personnel involved in work at height tasks, employers can promote a safer work environment and comply with regulatory requirements.
Inspection and maintenance of equipment
Regular inspections and maintenance of equipment used for work at height activities are crucial to ensure the safety and reliability of the equipment, minimising the risk of accidents and injuries.
Employers should establish inspection procedures that include:
-
- Pre-use inspections: Conducted by workers before using any equipment, such as ladders, scaffolds, or fall protection systems
- Periodic inspections: Performed by competent and responsible persons at regular intervals, as specified by the manufacturer or regulatory requirements.
Maintenance procedures should involve:
-
- Following manufacturer guidelines for maintenance and repairs
- Regularly checking equipment for wear, damage, or defects
- Removing faulty equipment from service until properly repaired or replaced
By implementing systematic inspection and maintenance procedures, employers can ensure the safety and reliability of equipment used in managing work at height activities, reducing the risk of accidents and promoting a safer work environment.
Managing work at height permits digitally
Digital permits to work represent a significant advancement in managing safety for work at height activities. These systems enable streamlined application processes, real-time monitoring, and improved record-keeping. Employers can submit and process permit applications online, allowing for faster approvals and immediate dissemination of permit conditions to all relevant parties. Permit to work software (PTW) also facilitate easier updates to work conditions and permit extensions, ensuring that all data is current and accessible. Key benefits include enhanced visibility of operations, reduced paperwork, and improved compliance tracking. This digital approach not only boosts efficiency but also significantly enhances safety by ensuring that critical safety information is instantly available and actionable by all stakeholders involved.
Adopting digital solutions for managing work at height (WAH) activities, alongside rigorous adherence to regulations and safety protocols, offers a comprehensive strategy to safeguard workers and minimise risks. The transition to digital permit to work systems exemplifies how technology can streamline safety management processes, promote a culture of safety, and maintain the highest standards of workplace safety.
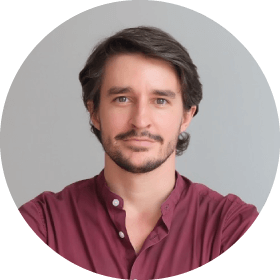
Axel oversees the customer success team at Novade. He has orchestrated the transformation of processes for hundreds of clients globally, and his deep industry knowledge and practical know-how have established him as a recognised authority in digital solutions implementation.
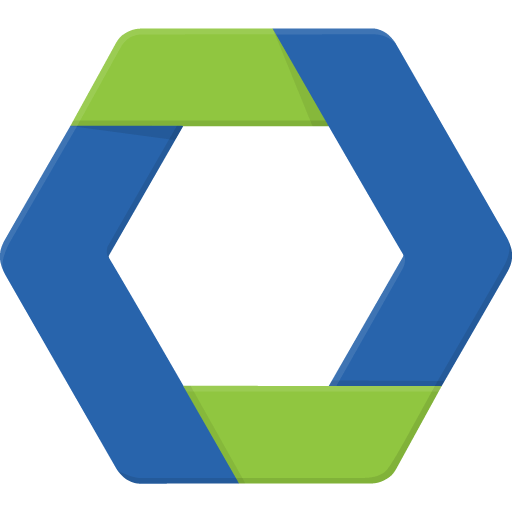
Novade is the market leader for the digitisation of safety field processes. Every day, clients around the world rely on Novade applications to manage the submission, approval, monitoring, and analysis of millions of digital permits to work.
Recommended content
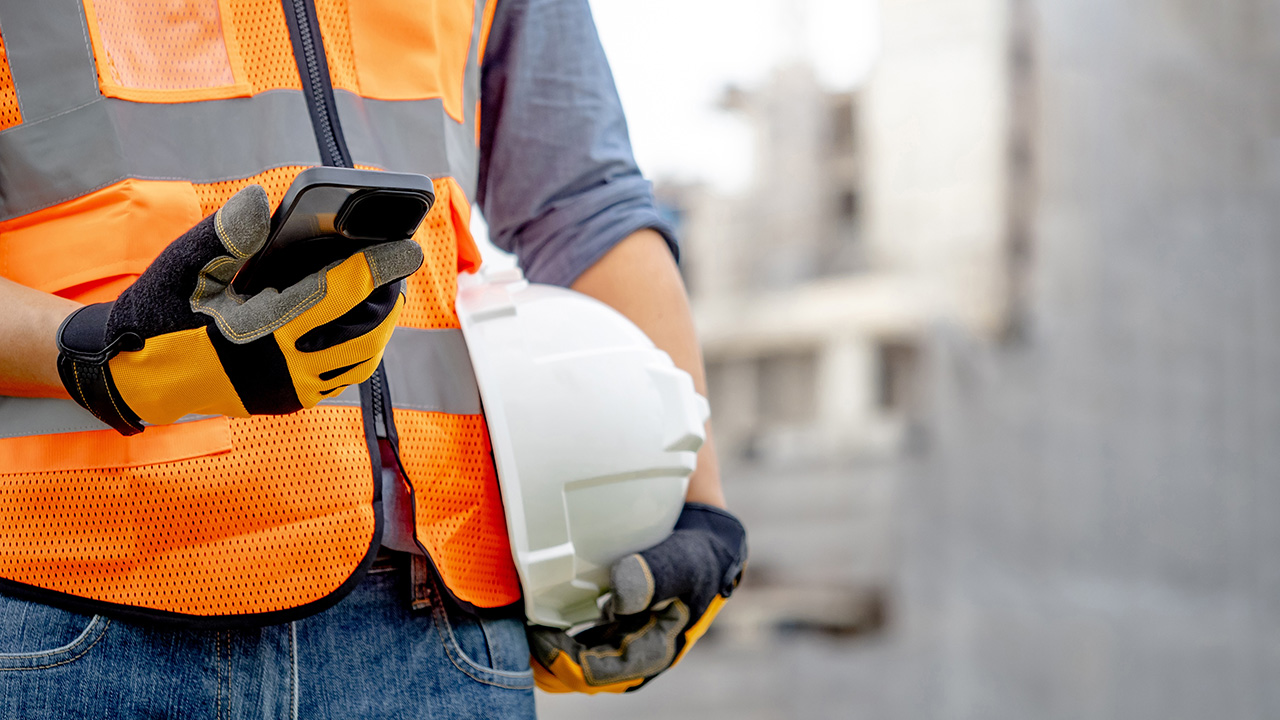
Novade’s Permit to Work software
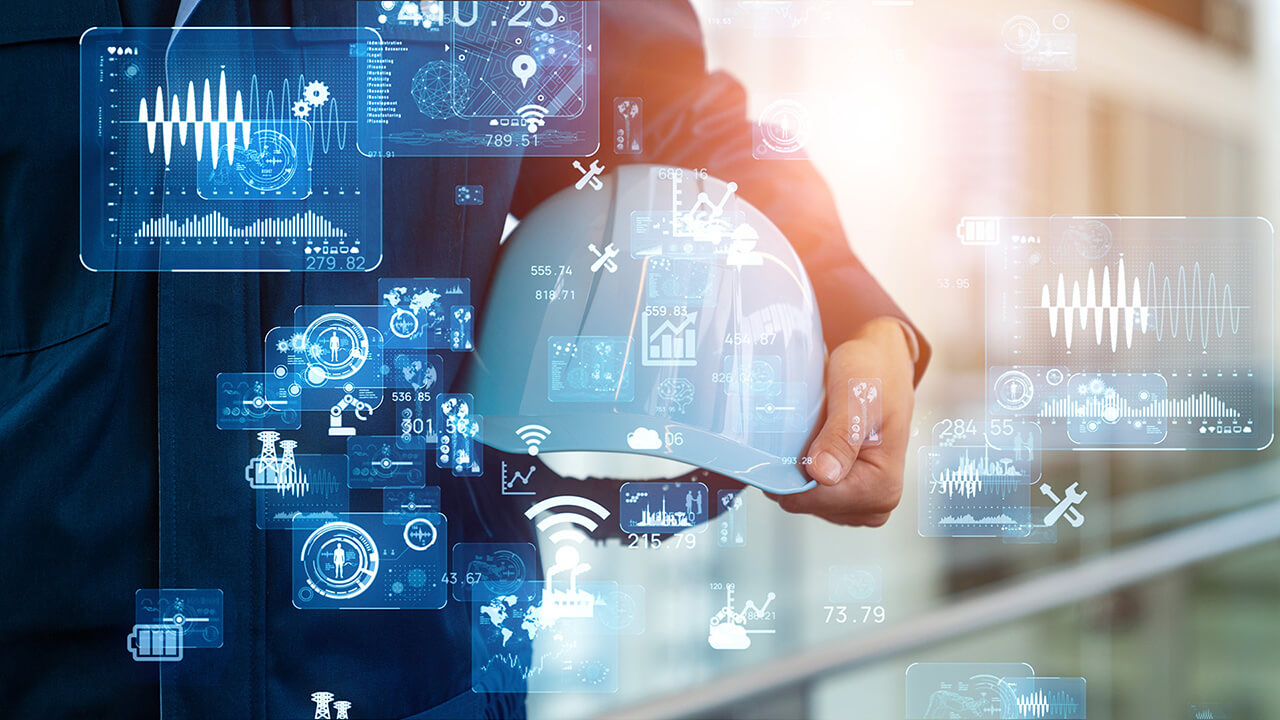
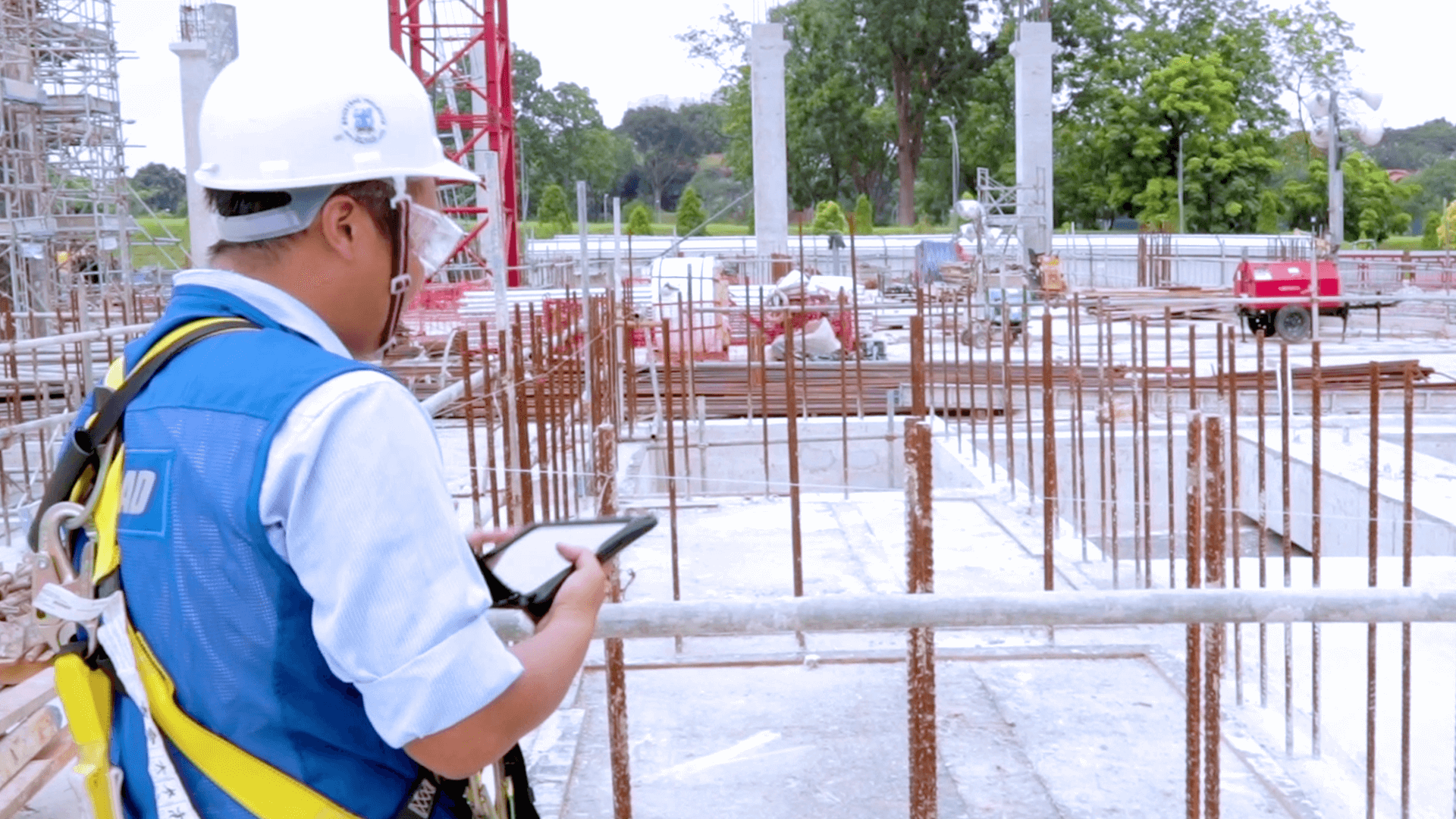
Subscribe to our newsletter