Improve quality management in construction with AI
Subscribe to our newsletter
Get the latest updates, trends and news directly in your inbox.
Quality plays a pivotal role in the construction industry. Poor project quality, in particular, is behind everything from safety problems to project budget blowouts. While putting a price on quality can be difficult, estimates suggest it falls between 5% and 20% of project construction costs. Artificial intelligence (AI) promises to help us better understand the cost of quality, give us more control over the quality management process, and lower costs.
Quality issues in construction projects are typically broken down into failures detected before handover and those identified after handover. Failures found before handover are within the builder’s control. However, these rework costs are often underestimated and rarely reflect total labour costs or costs of subsequent project delays.
On the other hand, those identified after handover have the potential to harm a contractor’s reputation as well as their ongoing client relationships. Both failures represent missed opportunities for all organisations involved.
Take an example of a 500-unit residential complex. It is not uncommon for projects of this scale to have 20 issues logged per unit. This adds up to 10,000 issues on the punch list to be identified, monitored, remedied, and closed out by various rounds of people. The compounding effects of less-than-quality work can be eye-watering.
Automating field inspections is just the start
The progressive automation of field inspections is increasing efficiencies and improving the quality control (QC) process. By analysing data captured in the field, quality issues are starting to be more predictable. Over time, and with the assistance of AI, they are likely to be preventable. AI technology will provide construction companies with more structured data to make quicker, more informed, and insightful decisions.
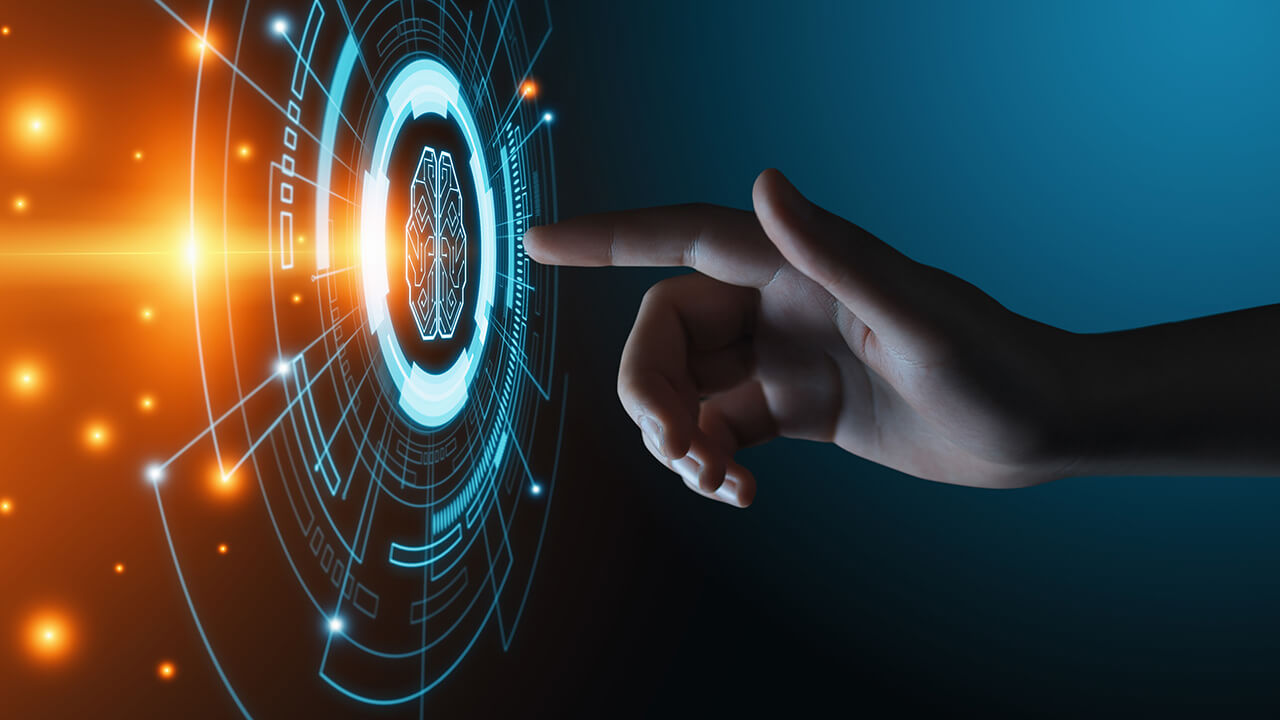
People and AI as on-site partners
Identifying defects, investigating specifics, and recording details in software solutions can be tedious and labour-intensive activities. Defects can be easily missed, poorly tracked, or inaccurately reported if inspectors are overwhelmed, tired, or distracted.
In the not-too-distant future, using highly skilled quality inspectors to investigate and record handover issues will be a thing of the past. Instead, construction managers will arm team members with handheld devices mounted with optical sensors to do much of the work for them.
As each area is being inspected, real-time data will be captured and analysed on-site. Handheld equipment will see scratches on doors, shade variations on windows, or missing tile fragments on the floor.
A 3D laser will take measurements and check dimensional conformities, identifying imperfect walls, wrongly positioned pipes, or improperly fitted appliances. An infrared camera will detect abnormal heat patterns and spot insulation defects. An X-ray camera will visualise faulty steel reinforcement in concrete beams.
An AI solution does not suffer fatigue or get stressed. It has superior sensory and visual perceptions, making it a valuable tool for project management and handovers. At the moment, however, an AI solution needs to be trained to understand processes and expectations.
AI tools cannot recognise results without being given examples of an object, shape, colour, defect, or imperfection. Once properly trained, AI will work tirelessly, quickly, and effectively to detect issues and follow processes.
What might the future hold?
Further into the future, instead of mounting sensors on handheld devices, they will be fitted to robots, or perhaps to autonomous vehicles. Inspections will be highly productive and comprehensive while removing all risks taken by humans.
Drones might fly up and down external walls of high-rise buildings, looking for cracks in façades, defects in paint jobs, or issues on roofs. Robots may roam around the construction site, constantly moving up and down the stairs, venturing near open edges, walking over or under obstacles, and safely exploring hazardous areas. All the while, cameras systematically scan the site ensuring everything is in order.
Digital solutions underpin the process
Once digitalised, quality issues can be automatically entered into rectification workflows. The quicker a quality issue is solved and closed, the lower its impact on the overall project cost and schedule. Think of the benefit of detecting and fixing water leaks in new residential units before plastering is done. Imagine the difference in effort, relationships, and costs if the issue was not found until damp started to appear as the project continued.
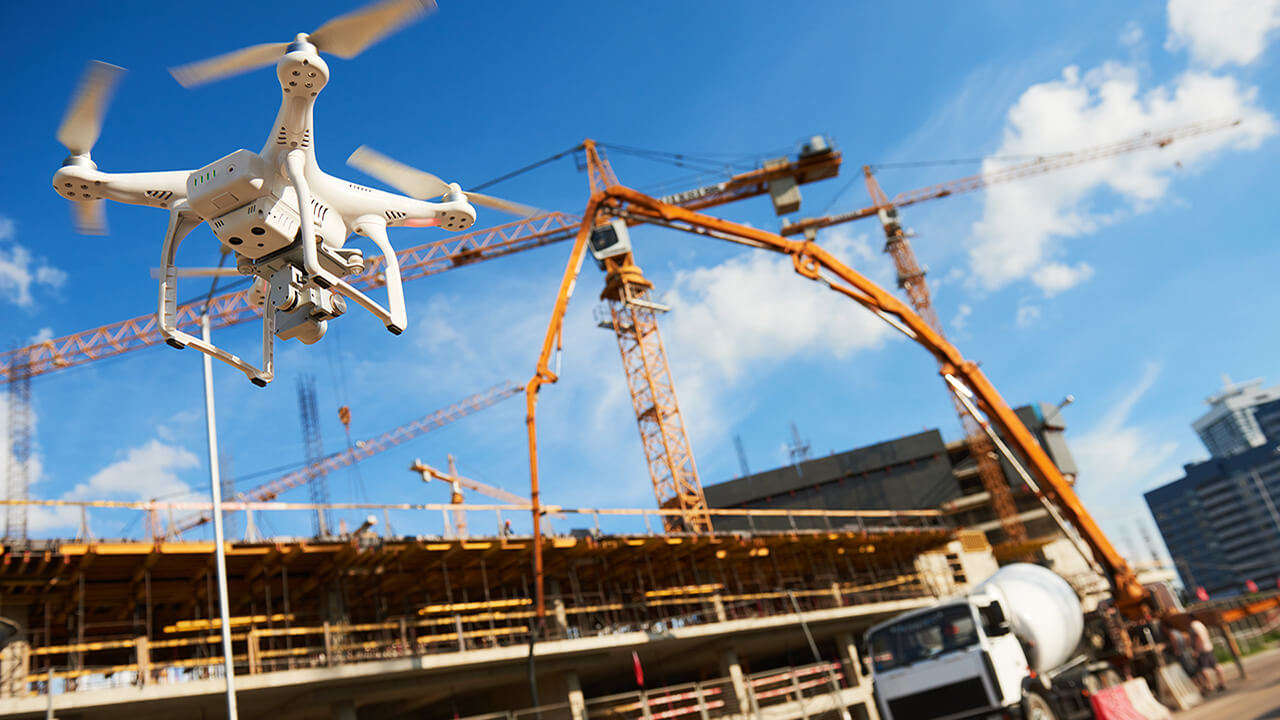
Using analytics to save time and money
Traditional data science extracts valuable insights from non-quality data and describes what has happened using descriptive analytics. Questions might include: Which construction quality issues are the most common? How long does remedial action take on average, and in extreme cases?
Which contractors or workers generate the most issues? Do we have a task problem or a labour one? Action plans are created from the answers to these questions.
AI and advanced analytics yield more sophisticated information to drive continuous improvement. For instance, using clustering techniques, AI might group issues in novel categories and provide several completely new perspectives, each requiring an action plan.
By analysing numerous input variables and finding data patterns, AI might alert leaders to issues:
- that were either previously overlooked by team members, or
- where the subtle signals are not yet detectable to managers.
The advanced warning can then be used to take preventative measures, fine-tune or reset equipment, change the material used, adjust procedures and work packages, or retrain or replace labour.
Once an issue has taken place, a trained AI algorithm can forecast the remedial time and cost. Combined with the scheduling AI, it can measure the impact on the overall schedule and decide on the resources required to fix the issue.
This article is based on the Novade AI whitepaper “How AI will Revolutionise Construction Site Management”.
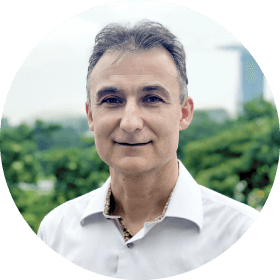
Denis is the founder and CEO of Novade and believes in a hands-on approach to building projects. A business leader with a track record in building global teams, Denis grew up in France, obtained his Master of Science degree at MIT, and previously worked at Autodesk as VP of Emerging Markets and APAC. He remains a firm believer in the ‘get it done’ philosophy.
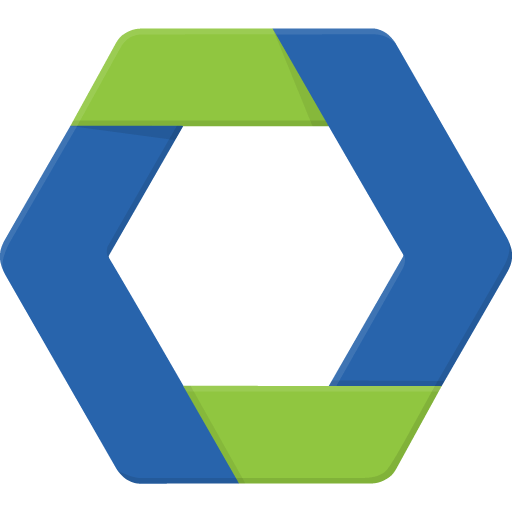
Novade has a team of digital specialists dedicated to supporting clients in their digital transformation from the ground up. With global experience on a wide range of construction projects and processes, the team will be able to quickly adapt to your needs from specification through to delivery and on-site support.
- Learn more about Novade’s digital construction platform
- Learn more about Novade Insights
- Learn more about Novade Quality
- Learn more about Novade’s construction management software
The rise of AI in construction management
The rise of AI in construction managementFeatured topics: Introduction: Why AI matters in construction What Is AI and how does it apply to construction? Key use cases of AI in construction management What’s needed to make AI work on site? Common myths and challenges...
Introduction to safety management system
Introduction to Safety Management System (SMS)Featured topics: What is a Safety Management System? Why a Safety Management System matters Safety Management System: The four key elements Why different industries need a tailored approach Common challenges in...
Trends in construction software in Thailand
Construction software trends in ThailandInsights from Khun Pasas, CEO of VR Digital Interview by Denis Branthonne During a recent visit to Bangkok, I had the pleasure of sitting down with Khun Pasas, the Director and Founder of VR Digital. VR Digital is a leading...
The rise of AI in construction management
The rise of AI in construction managementFeatured topics: Introduction: Why AI matters in construction What Is AI and how does it apply to construction? Key use cases of AI in construction management What’s needed to make AI work on site? Common myths and challenges...
Introduction to safety management system
Introduction to Safety Management System (SMS)Featured topics: What is a Safety Management System? Why a Safety Management System matters Safety Management System: The four key elements Why different industries need a tailored approach Common challenges in...